When it comes to additive manufacturing, Fused Deposition Modeling (FDM) has emerged as a game-changer, offering a wide array of possibilities across different industries. Let's delve into the potential applications of FDM printing and how it is revolutionizing various sectors.
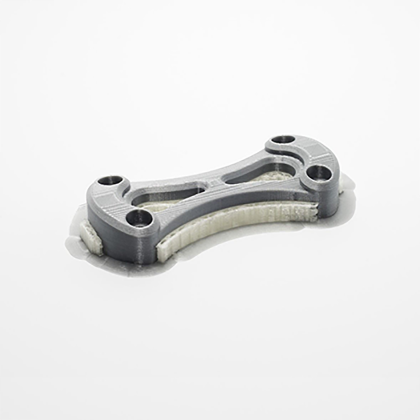
The Impact of FDM Printing in Manufacturing
FDM printing has significantly impacted the manufacturing industry by enabling rapid prototyping and production of complex geometries. Manufacturers can now create functional prototypes and end-use parts with reduced lead times and costs. This technology has streamlined the product development process, allowing for iterative design improvements and customization.
For example, in the automotive industry, FDM printing is used to produce lightweight and durable components, such as interior panels and brackets. This not only reduces the overall weight of vehicles but also enhances fuel efficiency. Similarly, in the aerospace sector, FDM-printed parts are utilized for creating lightweight yet robust components, contributing to the development of next-generation aircraft and spacecraft.
Advancements in Medical Applications
Exploring the Possibilities of FDM Printing in Various Industries has also made significant strides in the medical field. From creating patient-specific implants to manufacturing surgical tools and anatomical models, FDM printing has revolutionized the way medical devices are produced. This technology has opened new frontiers in personalized healthcare, allowing for the fabrication of tailored solutions for individual patients.
Orthopedic implants, such as hip and knee replacements, can now be custom-designed and 3D printed using FDM technology to match the patient's unique anatomy, leading to better outcomes and improved patient satisfaction. Additionally, medical researchers are exploring the use of FDM printing to develop tissue engineering scaffolds and drug delivery systems, paving the way for innovative treatments and therapies.
Enhancing Architectural and Construction Practices
Architects and construction firms are increasingly embracing FDM printing to explore innovative design possibilities and construction techniques. This technology allows for the fabrication of intricate architectural models, building components, and even entire structures with enhanced precision and efficiency. By harnessing the potential of FDM printing, architects can materialize their creative visions and push the boundaries of traditional construction methods.
Furthermore, FDM-printed concrete is gaining traction in the construction industry, enabling the rapid construction of complex geometries and sustainable structures. This approach not only reduces material wastage but also offers greater design freedom, leading to the development of more sustainable and aesthetically pleasing buildings.
Expanding Horizons in Consumer Goods
The consumer goods industry has also witnessed the transformative impact of FDM printing, with companies leveraging this technology to produce customized products and innovative designs. From personalized fashion accessories to bespoke home decor items, FDM printing has empowered brands to offer unique and tailored experiences to consumers.
Moreover, FDM printing has facilitated the development of sustainable and eco-friendly consumer goods by utilizing biodegradable materials and minimizing production waste. This aligns with the growing demand for environmentally conscious products and reinforces the role of FDM printing in shaping the future of consumer goods manufacturing.
In conclusion, the potential applications of FDM printing across various industries are vast and continually evolving. As technology advances and material capabilities expand, the impact of FDM printing will only continue to grow, driving innovation and reshaping traditional manufacturing practices.